2 Tips to Help Manage Costs When Signing a Long-Term Lease or Building a New Warehouse
By James (Jay) Rigelsky on Aug 15, 2019
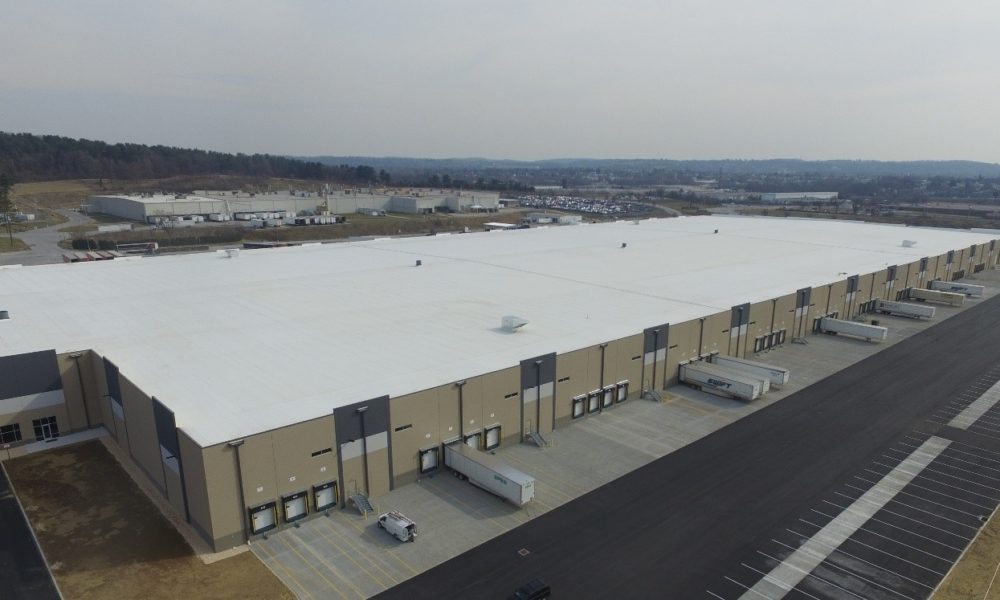
If your single or multi-warehouse operation is not currently meeting your existing and projected operational growth and logistic strategy, it may be time to consider building or leasing a new facility.
During your annual operational strategy review and budget planning meetings, do you and your leadership team look at warehouse operation(s) and facility, or facilities, and see:
- Congested warehouse(s), walls and floor damages?
- Insufficient lighting that has increased costs, reduced productivity and raised safety concerns?
- Increased repair calls that place a “band-aid” on essential repairs and/or replacements of operating and production systems?
- Amplified expenses associated with those repair calls because there is no more space to relocate and store product while repairs are being completed, and the contractor must “work around” the congested warehouse or freezer-cooler floor space?
While there are numerous steps to consider when building or leasing a new commercial freezer, cooler, or warehouse space, we’ve examined two critical areas to recognize when upgrading your current facility.
Follow these tips to avoid common omissions and oversights:
1. Avoid Unnecessary Construction:
After conducting a thorough evaluation of your existing facility, consider all your existing and “new” product SKUs, prioritize the same based on how frequently the SKUs turn, and commence an inside out “planning phase” with a qualified architect and commercial real estate expert. The inside out planning phase should begin with the distribution area (floor operations), or freezer and cooler area and flow outward. This inside out planning approach will improving your operations and efficiency, which will help you avoid constructing unnecessary square footage, or paying for high-priced change orders. It doesn’t matter how many box trucks, over-the-road haulers, 53-foot trailers, and modified trailers you can park or store, if you can efficiently position the logistical assets around a strategically planned floor operation that allows you to efficiently receive and distribute your newly prioritized products.
2. Additional Operation Planning Considerations:
Although it may seem perfectly logical to locate a newly constructed or long term leased warehouse or freezer/cooler warehouse adjacent to a store or stores, there are several cost factors you should consider that may measurably reduce construction costs. Some of the more important cost reduction factors to consider are land cost and availability in relation to your entire distribution/service region, zoning designations, and time and costs associated with changing zoning designations, if necessary, and over-the-road truck access to interstates. It is important to keep in mind your newly constructed or long-term leased warehouse should be constructed with at least a 120 foot truck court to improve maneuverability of over-the-road haulers with 53-foot trailers entering and leaving your warehouse.
As discussed above, after thoroughly assessing distribution operations, plan for:
- Sufficient number of dock positions
- Include as many dock positions as possible in your construction plans, even if you do not build out all the positions.
- The various dock position sizes and heights to consider are dock heights of 48-50 inches for over the road haulers, and possibly a few dock positions ranging from 36, 42 and 48 inches for specific delivery trailers and special use trucks.
- Determine dock height positions – will all trucks be the same size?
- Parking for trucks, drop trailers, employees, customers and visitors – Does the “flow” facilitate or inhibit your newly developed strategic operations’ plan?
In addition to being mindful of these two items, it is critical to engage a commercial real estate expert to help ensure your success in acquiring your new warehouse space. CRA has a proven process and extensive experience in warehousing and freezer/cooler design needs and efficiencies, logistical planning, and proficiency in representing a tenant’s needs, not a landlord’s.